By Marisabel Caballero, Global Technical Manager Poultry, EW Nutrition
COVID-19 and its aftermath, the Russia-Ukraine war, and climate change have all contributed to the current crisis. Energy price increases, supply chain difficulties, and raw material availability and rising prices are all consequences felt deeply across the animal production sector. It is now time that the industry puts in place mitigation plans and starts taking action.
Cost and availability of fats – a looming problem
The lockdowns during the COVID-19 pandemic in 2019/2020 caused a rapid drop in energy demand and therefore a cut in global oil production. In 2021, as normality was recovered, it was met an energy supply-demand imbalance leading to a global supply chain crisis that further stressed the delivery of energy sources. In 2022, one of Europe’s driest summers compounded by the Russian-Ukrainian war have greatly contributed to the increasing energy prices.
With two of the largest suppliers of grains and oil – Russia and Ukraine – at war, the global food supply and prices are also compromised. These two countries provide the world with more than 20% of all wheat and barley, 15% of corn and 60% of sunflower oil (FAO, 2022).
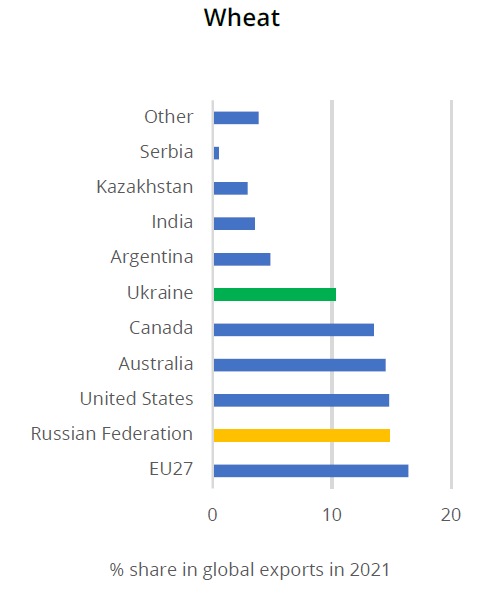
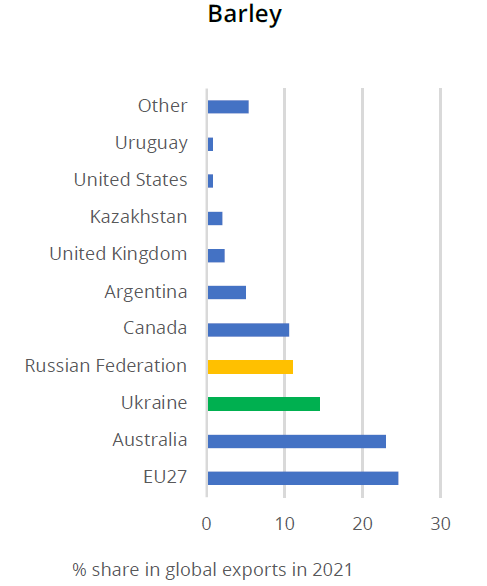
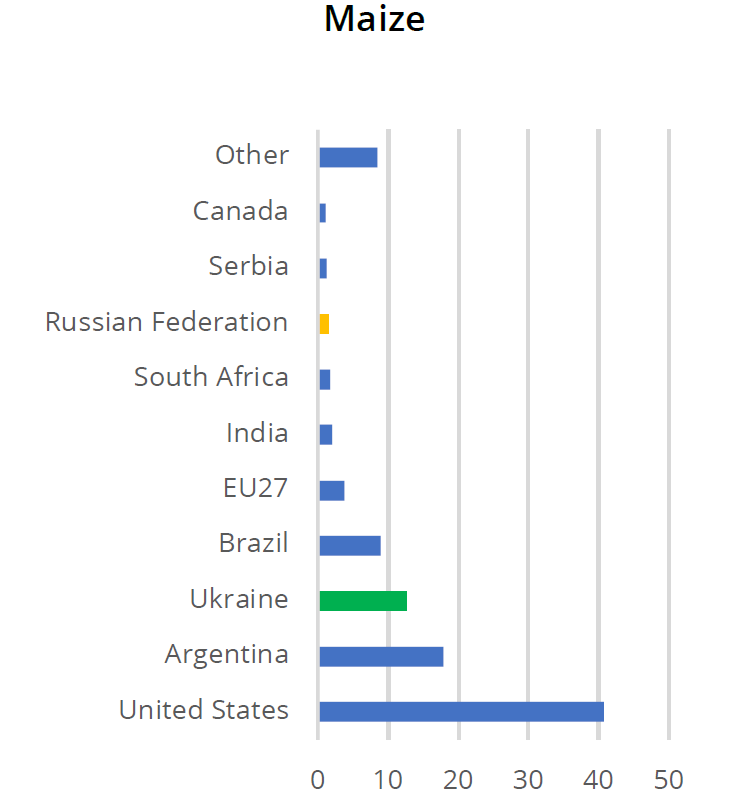
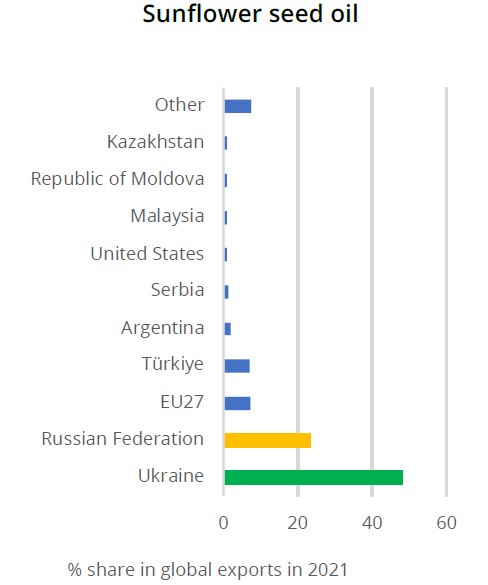
Moreover, corn and soybean yields in South America also fell sharply in 2019-20 and 2021-22 due to the impact of La Nina and are expected to continue being low in the next season.
Biofuels and animal production compete for crops
Biofuels have been seen as a solution to decrease fossil-fuel energy dependance. Before the war, global biofuel production was at a record high. However, in the current crisis, biofuels may be a contributor to the rise in food prices, as they use a significant percentage of feed-production crops. Only in the US, around 30% of the corn production goes into biofuels, while biodiesel accounts for 40% of soybean oil use (O’Malley & Searle, 2021).
For the animal production industry, maintaining performance and profitability during price hikes involves a combination of strategies. Feed production accounts for up to 70% of meat production costs. With the soaring energy and raw material crisis, feed production costs are on the spot.
The impact of fat in pelleting process output
Oils and fats generally are added to animal feeds as a rich source of energy and other essential nutrients. For the feed production unit, fats can be a pellet quality and energy output enhancer.
During the pelleting process, fat can increase production output, save energy, and prolong the production life of the die as it can act as a lubricant during the process. The feed ingredients contain fat, and a portion of fat/oil is usually added in the mixer. Too much in-mixer fat addition (higher than 2%) negatively affects pellet quality, and when fat is too low (no addition), the production rate decreases. Fats and oils are also added through a pellet coating system, which has been demonstrated to improve pellet quality.
In fats/oils high cost and shortage scenarios, feed production managers and nutritionists are faced with the challenge of production with higher constraints. In-mixer fat addition has consequences in throughput. However, in-mixer moisture addition facilitates conditioner steam penetration into the feed particles. With that, the efficiency of the process may be partially recovered.
Solving the efficiency & quality equation
Simply adding water into the mixer does not give optimal results: Surfactants, on the other hand, improve moisture penetration into the feed particles and increase lubrication at pellet die point. By reducing the surface tension of water, surfactants enable the feed particles to absorb and distribute the moisture uniformly.
Improved moisture retention facilitates the starch gelatinization during mash conditioning and passing through the pellet die. This is important to make the pellet more durable and the feed more digestible. It also reduces friction and hence the energy required for the pelleting process (improving milling efficiency). At the same time, surfactants aid with pellet water retention, minimizing feed shrinkage without increasing water activity, thus curbing feed microbial growth.
What difference can an effective surfactant make?
The effect of adding SURF•ACE to diets with different levels of fat was evaluated in more than 40 feed mills, with production capacities ranging from 5 to 20 tons per hour. SURF•ACE is added to water sprayed during mixing. This solution lubricates the mash feed, improves steam penetration and starch gelatinization, and thus reduces friction in the pellet die. The results show that, relative to pure water, the addition of SURF•ACE increases press throughout (t/h) by up to 25%.
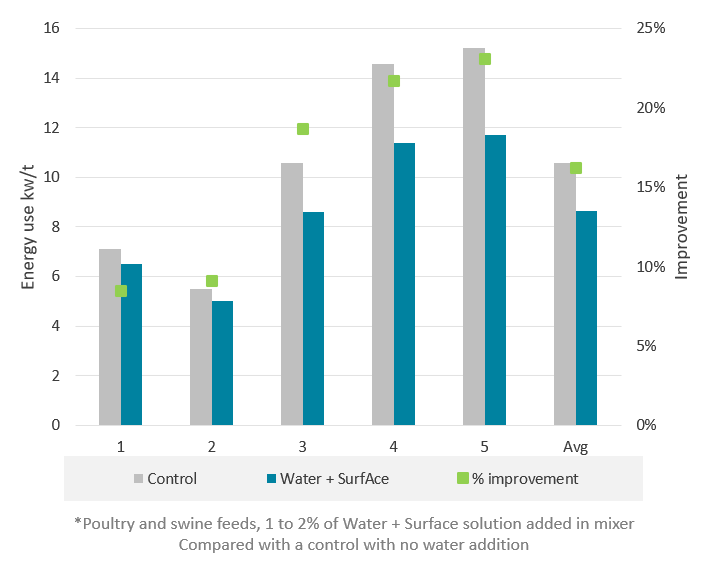
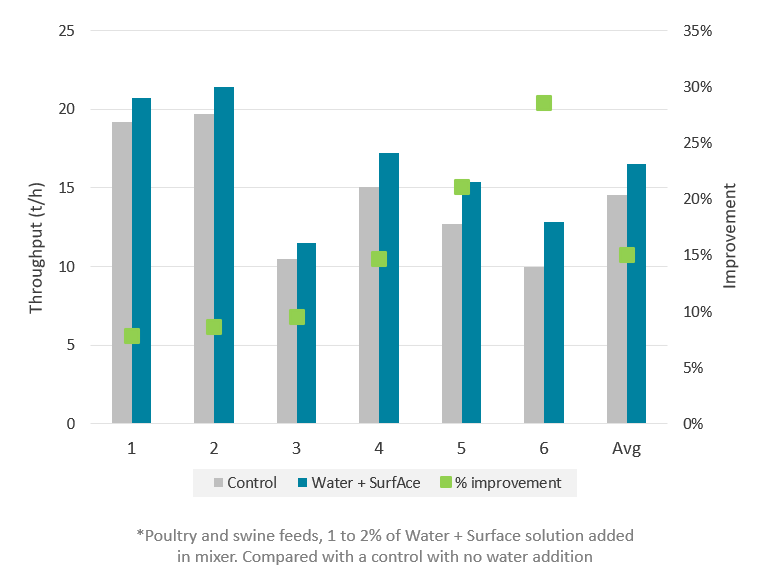
Prioritize efficiency to compensate current challenges
Operating in a tight margin environment, feed mills always need to prioritize efficiency. The advantages of using SURF•ACE feed mill processing aid are clear: reduced energy consumption without compromising pellet quality; moisture optimization; and higher productivity.
During times of increasingly high ingredient and energy costs, it is even more important to utilize savings opportunities at every production stage.