By Vaibhav Gawande, Assistant Manager Technical Services, Dr. Inge Heinzl, Editor, and Technical Team, EW Nutrition
The utility value of feed consists of the nutritional value and the quality. The first covers all characteristics concerning the essential nutrients and is important for feed formulation and the adequate supply of the animals.
Feed quality comprises all characteristics of a feed influenced by treatment, storage, conservation, hygiene, and its content of specific substances. For many factors, guidance and threshold values are available which should be met to guarantee animal health and welfare, as well as to protect public health, since some undesirable substances can be transferred to animal products such as meat, eggs, and milk.
In this article, we will focus on feed hygiene. We will talk about the consequences of low feed quality, how to understand it, its causes, and possible solutions.
What are the effects of deficient feed hygiene?
The consequences of deficient feed hygiene can be divided into two parts, impurities and spoilage.
Impurities comprise:
- the presence of soil, sand, or dust
- contamination with or residues of heavy metals, PCB, dioxins, pesticides, fertilizers, disinfectants, toxic plants, or banned feed ingredients
In the case of spoilage, we see:
- degradation of organic components by the action of molds and bacteria
- growth of pathogens such as E. coli, salmonella, etc.
- accumulation of toxins such as mycotoxins or bacterial toxins (Hoffmann, 2021)
Bad feed hygiene can also negatively impact the feed’s nutritional value by leading to a loss of energy as well as decreasing the bioavailability of vitamins A, D3, E, K, and B1.
But, how can all signs of deficient feed hygiene be recognized? Soil, sand, and probably dust can be seen in well-taken samples and impurities can be analyzed. But is it possible to spot spoilage? In this case, agglutinated particles, rancid odor, moisture, and discoloration are indicators. Sometimes, also the temperature of the feed or ingredient increases. However, spoilage is not always obvious and an analysis of the feed can give more information about the spoilage-related organisms present. It also helps to decide if the feed is safe for the animals or not. In the case of obvious alterations, the feed should not be consumed by any animal.
Different organisms decrease feed quality and impact health
Several organisms can be responsible for a decrease in feed quality. Besides the visible pests such as rats, mice, or beetles, which can easily be noticed and combatted, there are organisms whose mastering is much more difficult. In the following part, the different harmful organisms and substances are described and solutions are presented.
Enteropathogens can cause diarrhea and production losses
In poultry, different bacteria responsible for high production losses can be transferred via the feed. The most relevant of them are Clostridium perfringens, Escherichia coli, and some strains of Salmonella.
Clostridium perfringens, the cause of necrotic enteritis
Clostridium perfringens is a Gram-positive, anaerobic bacterium that is extremely resistant to environmental influences and can survive in soil, feed, and litter for several years and even reproduce. Clostridium perfringens causes necrotic enteritis mainly in 2-16 weeks old chickens and turkeys, being more critical in 3-6 weeks old chicks.
There is a clinical and a subclinical form of necrotic enteritis. The clinical form can be detected very well due to clear symptoms and mortality rates up to 50%. The subclinical form, while harder to detect, also raises production costs due to a significant decrease in performance. The best prophylaxis against clostridia is the maintenance of gut health, including feed hygiene.
Clostridia can be found in animal by-products, as can be seen in table 1.
Sr. No. |
Sample details |
Clostridium perfringens contamination |
Total number of samples |
Positivity % |
Positive |
Negative |
1 |
Meat and bone meal |
39 |
52 |
91 |
42.86 |
2 |
Soya meal |
0 |
3 |
3 |
0 |
3 |
Rape seed meal |
0 |
1 |
1 |
0 |
4 |
Fish meal |
21 |
17 |
38 |
55.26 |
5 |
Layer Feed |
21 |
71 |
93 |
22.58 |
6 |
Dry fish |
5 |
8 |
13 |
38.46 |
7 |
De-oiled rice bran |
0 |
2 |
2 |
0 |
8 |
Maize |
0 |
2 |
2 |
0 |
9 |
Bone meal |
13 |
16 |
29 |
44.83 |
Table 1: Isolation of Clostridium perfringens from various poultry feed ingredients in Tamil Nadu, India (Udhayavel et al., 2017)
Salmonella is harmful to animals and humans
Salmonella is a gram-negative enterobacterium and can occur in feed. There are only two species – S. enterica and S. bongori (Lin-Hui and Cheng-Hsun, 2007), but almost 2700 serotypes. The most known poultry-specific Salmonella serotypes are S. pullorum affecting chicks and S. gallinarum affecting adult birds. The other two well-known serotypes, S. enteritidis and S. typhimurium are the most economically important ones because they can also infect humans.
Salmonella enteritidis, in particular, can be transferred via table eggs to humans. The egg content can be infected vertically as a result of a colonization of the reproductive tract of the hen (De Reu, 2015). The other possibility is a horizontal infection, as some can penetrate through the eggshell from a contaminated environment or poor egg handling.
Salmonella can also be transferred through meat. However, as there are more production steps where contamination can happen (breeder and broiler farm, slaughterhouse, processing plants, food storage…), traceability is more complicated. As feed can be vector, feed hygiene is crucial.
Moreover, different studies have found that the same Salmonella types found in feed are also detected – weeks later – in poultry farms and even further in the food chain, as reviewed by Ricke and collaborators (2019). Other researches even imply that Salmonella contamination of carcasses and eggs could be significantly reduced by minimizing the incidence of Salmonella in the feed (Shirota et al., 2000).
E. coli – some are pathogenic
E. coli is a gram-negative, not acid-resistant bacterium and most strains are inhabitants of the gut flora of birds, warm-blooded animals, and humans. Only some strains cause disease. To be infectious, the bacteria must have fimbriae to attach to the gut wall or the host must have an immune deficiency, perhaps due to stress. E. coli can be transmitted via contaminated feed or water as well as by fecal-contaminated dust.
Escherichia coli infections can be found in poultry of all ages and categories and nearly everywhere in the bird. E. coli affects the navel of chicks, the reproductive organs of hens, several parts of the gut, the respiratory tract, the bones and joints, and the skin and are part of the standard control.
The feed microbiome can contribute to a balanced gut microbial community. The origins of pathogenic E. coli in a flock can also be traced to feed contamination (Stanley & Bajagai, 2022). Especially in pre-starter/starter feeds, E. coli contamination can be critical as the day-old chick’s gut is starting to be colonized. Especially in this phase, maintaining a low microbial count in feed is crucial.
Molds cause feed spoilage and reduce nutritional value
Molds contaminate grains, both in the field and during storage, and can also grow in stored feed and even in feed stored or accumulated in storage facilities in animal production farms.
The contamination of feed by molds and their rapid growth can cause heating of the feed. As molds also need nutrients, their growth results in a reduction of energy and the availability of vitamins A, D3, E, K, and B1, thus decreasing the feed’s nutritional value. This heating occurs in most feeds with a moisture content higher than 15 /16%. Additionally, mold-contaminated feed tends to be dusty and has a bad taste impacting palatability and, as a consequence, feed intake and performance.
Molds produce spores that can, when inhaled, cause chronic respiratory disease or even death if the animals are exposed to contaminated feed for a longer time. Another consequence of mold contamination is the production of mycotoxins by several mold species. These mycotoxins can affect the animal in several ways, from decreasing performance to severe disease (Esmail, 2021; Government of Manitoba, 2023).
With effective feed hygiene management, we want to stop and prevent mold growth, as well as all its negative consequences.
Prevention is better than treatment
It is clear that when the feed is spoiled, it must be removed, and animal health supporting measures should take place. However, it is better to prevent the consequences of low feed hygiene on animals. Proper harvest and adequate storage of the feed are basic measures to stop mold growth. Additionally, different tools are available to protect the animals from feed bacterial load and other risk factors.
Solutions are available to support feed hygiene
There are several solutions to fight the organisms which decrease feed quality. Some directly act against the harmful substances / pathogens, and others act indirectly, meaning that they change the environment to a non-comfortable one for the organism.
Formaldehyde and propionic acid – an unbeatable team against bacteria
A combination of formaldehyde and propionic acid is perfect to sanitize feed. Formaldehyde results in bacterial DNA and protein damage, and propionic acid is active against bacteria and molds. Together, they improve the microbiological quality of the feed and reduce the risk of secondary diseases such as necrotic enteritis or dysbiosis on the farm. In addition to the pure hygienic aspect, organic acids support digestion.
An in-vitro trial was conducted to evaluate the effect of such a combination (Formycine Gold Px) against common poultry pathogens. Poultry feed was spiked with three different bacteria, achieving very high initial contamination of 1,000,000 CFU/g per pathogen. One batch of the contaminated feed served as a control (no additive). To the other contaminated batches, 1, 2, or 4 kg of Formycine per ton of feed were added. The results (means of triplicates) are shown in figures 1 a-c.
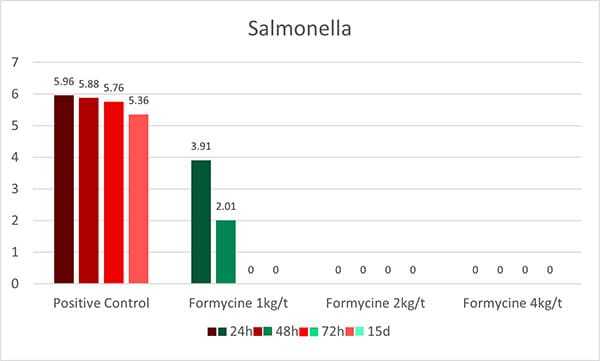
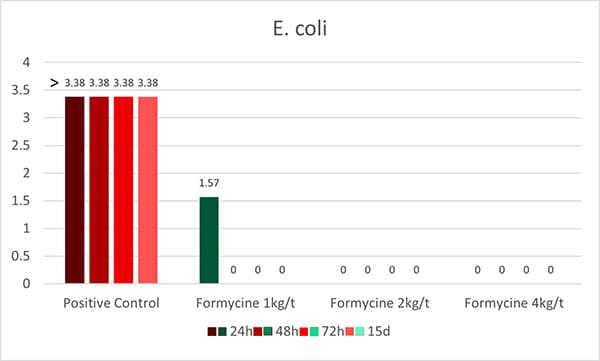
Figures 1 a-c: Reduction of bacterial count due to the addition of Formycine
Formycine Gold Px significantly reduced the bacterial counts in all three cases. A clear dose-response-effect can be seen and by using 2 kg of Formycine / t of feed, pathogens could not be detected anymore in the feed.
A further trial showed the positive effects of feeding Formycine Gold Px treated feed to the animals. Also here, the feed for both groups was contaminated with 1,000,000 CFU of Clostridium/g. The feed of the control group was not treated and to the treatment group, 2 kg of Formycine per t was added.
Figure 2: Preventive effect of Formycine Gold Px concerning necrotic enteritis gut lesions
Figure 3a and 3b: Performance-maintaining effect of Formycine Gold Px
The trial showed that Formycine Gold Px reduced the ingestion of the pathogen, and thus could prevent the lesions caused by necrotic enteritis (Fig. 2). The consequence of this improved gut health is a better feed conversion and higher average daily gain (Fig.3a and 3b).
Products containing formaldehyde may represent a risk for humans, however, the adequate protection equipment helps to reduce/avoid exposure.
A combination of free acids and acid salts provides optimal hygienic effects
Additionally, another blend of organic acids (Acidomix AFG) shows the best effects against representatives of relevant feed-borne pathogens in poultry. In a test, 50 µl solution containing different microorganisms (reference strains of S. enterica, E. coli, C. perfringens, C. albicans, and A. niger; concentration 105 CFU/ml, respectively) were pipetted into microdilution plates together with 50 µl of increasing concentrations of a mixture of organic acids (Acidomix) After incubation, the MIC and MBC of each pathogen were calculated.
The test results show (figure 4, Minimal Bactericidal Concentration) that 0.5% of Acidomix AFG in the medium (≙ 5kg/t of feed) is sufficient to kill S. enterica, C. albicans, and A. niger and even only 2.5kg/t in the case of E. coli. If the pathogens should only be prevented to proliferate, even a lower amount of product is requested (figure 5, Minimal Inhibitory Concentration – MIC)
Figure 4: MBC of Acidomix AFG against different pathogens (%)
Figure 5: MIC of Acidomix AFG against different pathogens (%)
In addition to the direct antimicrobial effect, this product decreases the pH of the feed and reduces its buffering capacity. The combination of free acids and acid salts provides prompt and long-lasting effects.
Feed hygiene: a critical path to animal performance
Feed accounts for 65-70% of broiler and 75-80% of layer production costs. Therefore, it is essential to use the available feed to the utmost. The quality of the feed is one decisive factor for the health and performance of the animals. Proper harvesting and storage are in the hands of the farmers and the feed millers. The industry offers products to control the pathogens causing diseases and the molds producing toxins and, therefore, helps farmers save feed AND protect the health and performance of their animals.
References:
Dinev, Ivan. Diseases of Poultry: A Colour Atlas. Stara Zagora: Ceva Sante Animal, 2007.
Esmail, Salah Hamed. “Moulds and Their Effect on Animal Health and Performance.” All About Feed, June 17, 2021. https://www.allaboutfeed.net/all-about/mycotoxins/moulds-and-their-effect-on-animal-health-and-performance/.
Government of Manitoba. “Spoiled Feeds, Molds, Mycotoxins and Animal Health.” Province of Manitoba – Agriculture. Accessed March 16, 2023. https://www.gov.mb.ca/agriculture/livestock/production/beef/spoiled-feeds-molds-mycotoxins-and-animal-health.html.
Hoffmann, M. “Tierwohl Und Fütterung.” LKV Sachsen: Tierwohl und Fütterung. Sächsischer Landeskontrollverband e.V., January 25, 2021. https://www.lkvsachsen.de/fuetterungsberater/blogbeitrag/artikel/tierwohl-und-fuetterung/.
Ricke, Steven C., Kurt Richardson, and Dana K. Dittoe. “Formaldehydes in Feed and Their Potential Interaction with the Poultry Gastrointestinal Tract Microbial Community–A Review.” Frontiers in Veterinary Science 6 (2019). https://doi.org/10.3389/fvets.2019.00188.
Shirota, Kazutoshi, Hiromitsu Katoh, Toshihiro Ito, and Koichi Otsuki. “Salmonella Contamination in Commercial Layer Feed in Japan.” Journal of Veterinary Medical Science 62, no. 7 (2000): 789–91. https://doi.org/10.1292/jvms.62.789.
Stanley, Dragana, and Yadav Sharma Bajagai. “Feed Safety and the Development of Poultry Intestinal Microbiota.” Animals 12, no. 20 (2022): 2890. https://doi.org/10.3390/ani12202890.
Su, Lin-Hui, and Cheng-Hsun Chiu. “Salmonella: Clinical Importance and Evolution of Nomenclature.” Chang Gung Med J 30, no. 3 (2007): 210–19.
Udhayavel, Shanmugasundaram, Gopalakrishnamurthy Thippichettypalayam Ramasamy, Vasudevan Gowthaman, Shanmugasamy Malmarugan, and Kandasamy Senthilvel. “Occurrence of Clostridium Perfringens Contamination in Poultry Feed Ingredients: Isolation, Identification and Its Antibiotic Sensitivity Pattern.” Animal Nutrition 3, no. 3 (2017): 309–12. https://doi.org/10.1016/j.aninu.2017.05.006.