Conference report
In the Poultry Academy held by EW Nutrition in the fall of last year, Judy Robberts, Technical Service Manager, Aviagen, explained that the success of a breeder flock depends on producing good quality hatching eggs with high hatchability and delivering first quality chicks. With this in mind, we have to ask two essential questions: What impact does the breeder farm have on chick quality? And What are the most overlooked areas for breeders?
Nest box hygiene
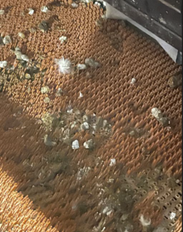
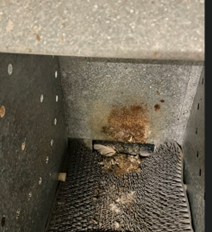
Nest box hygiene is key to good quality hatching eggs. Shortly after egg deposition, the eggshell is moist, and the cuticle is not yet an effective protection. In addition, during this period the egg is cooling down from the hen’s body temperature (41°C) to house temperature. Due to this process of cooling down, the content of the egg contracts and a vacuum is created in the egg. In compensation, air enters and forms the air cell. Together with this air, bacteria can easily penetrate the egg. For this reason, it is very important that only hatching eggs are used which have been laid in a clean nest.
Maintaining a hygienic nest environment with routine cleaning of the nest mat or frequently replacing the bedding material will reduce the risk of bacterial contamination.
Clean nests and nesting equipment are essential to avoiding contamination.
Egg collection and pick-up schedule
Collect nest eggs a minimum of 4 times a day, more frequently in hot weather, as eggs cannot cool down sufficiently in the house to interrupt embryonic development. Adjust the exact timing so that no more than 30% (any more will increase the incidence of cracked eggs) of the eggs fall in any one collection. When determining collection times, it is important to remember:
- The majority of eggs will be laid in the morning, and collection intervals should be managed accordingly.
- Eggs left in the nest or on belts longer than recommended will have an increased incidence of being cracked or soiled.
- Transition points on belts need to be smooth so eggs don’t pile up and bump into each other.
- Never leave eggs overnight in the nests or belts.
- Eggs left in conventional nests are subject to toe pecks or soiling from other hens.
- Floor eggs (eggs that were laid outside of the breeder flock’s next boxes) should be collected more often than nest eggs.
It is not advisable to collect eggs in cardboard egg trays/flats, as the fiber material absorbs egg heat, and it takes longer for them to cool down. Because the fiber trays are porous, they can also harbor unwanted organisms/bacteria/fungi and attract vermin.
Ideally hatching eggs should weigh a minimum of 50 g from a flock at least 22 weeks of age. Smaller eggs from younger flocks may be used, however, chick size and early livability will not be optimum. Remember that a chick will yield approximately 68% of the egg size. Therefore, a small egg will produce a small chick.
Egg cleanliness
Always wash hands after collecting floor eggs and before each collection of nest eggs. Floor eggs should not be placed in the nest box – even if they appear clean. Washing floor and dirty eggs removes the eggs protective coating. Always remember, a washed egg is still a dirty egg, but a clean egg is one that was never dirty.
Eggs should be treated with chemical-based antimicrobials, as scraping, rubbing, or washing the eggshell will damage the cuticle and remove the physical and antimicrobial barrier. Since the eggshell permeability increases after 24 hours and makes the eggs more susceptible to bacterial invasion, eggs should be sanitized as soon as possible. The most popular method is fogging as it is safe, the fog reaches all the eggs and the eggs do not get wet.
Floor eggs are not hatching eggs
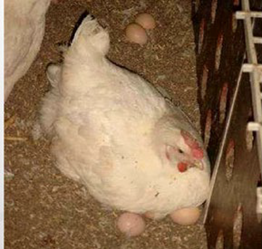
The hatchery cannot fix mistakes from the breeder farm. Therefore, it is NOT recommended to set floor eggs – eggs that were laid outside of the breeder flock’s next boxes. Floor eggs have a higher bacterial load than nest eggs and consequently lower hatchability. They are also potential ‘bangers, or exploders’ and can cross-contaminate other eggs, especially in the same incubator.
Selection of floor eggs must be done at the farm, so that a dirty egg never enters the hatchery. Where strictly necessary, set floor or dirty eggs only if the disadvantages of setting these eggs are fully understood and accepted by the hatchery. If floor eggs are used for hatching, they should be clearly marked and stored separately from the nest eggs so that the hatchery can manage the contamination risk appropriately.
Floor eggs have a significantly higher risk of microbial contamination that will reduce hatch and chick quality.
Egg hygiene – bacterial contamination
Egg condition |
Total Bacteria (cm2) |
Newly laid |
300 |
Cooled clean egg |
3,000 |
“Clean” floor egg |
30,000 |
Dirty egg |
300,000 |
Monitor the number of floor eggs and adjust management practices to minimize them. Floor eggs are a problem that should be tackled at the breeder level, with good breeder management and suitable housing equipment. If levels of floor eggs exceed 2-3% across the life of the flock, there is a problem. Floor eggs will be much higher at the start of production, but by peak production should be down to 1-2%.
Cracked eggs
Eggs with cracks are more likely to become infected and have low hatchability and poor chick quality.
Influence of eggshell crack types on hatchability and chick quality
Treatment |
Egg weight at transfer (g) |
Weight loss (%) |
Fertility (%) |
Hatchability (%) |
Chick weight (g) |
Chick uniformity (%) |
Normal |
62.0a |
11.4c |
97.8a |
83.9a |
48.9a |
82.6 |
Star cracks |
55.6b |
20.7b |
89.4b |
49.4b |
48.2a |
70.3 |
Hairline cracks |
53.1c |
24.0a |
83.3c |
30.0c |
45.6b |
70.2 |
Khabisi et al., 2011 a-c Means within a column without a common superscript differ significantly (p ≤ 0.05)
Do not set cracked eggs. Record the number of eggs with cracks, and if the frequency is unsatisfactory, investigate and eliminate possible causes.
On-farm egg storage rooms
Don’t forget that storage starts from the time of laying, not the time of receival at the hatchery.
Eggs need to be cooled below 24oC (threshold temperature or physiological zero) as soon as possible to stop cellular growth of the embryo, until the egg is set at the hatchery. This minimizes embryo mortality, maximizes hatchability and helps to ensure chick quality. Eggs should be stored within 4 hours after collection.
On breeder farms, eggs are usually stored until being transported to the hatchery. The storage duration depends on the egg room capacity, supply of hatching eggs, hatchery capacity, and demand for day-old chicks. Don’t forget that storage starts from the time of laying, not the time of receival at the hatchery.
If the farm has an environmentally controlled egg storage room, eggs can be collected by the hatchery at least twice a week. If the farm has no dedicated egg storage room, eggs must be transported to the hatchery daily. Uncontrolled fluctuations in egg storage temperatures will cause stop-start growth of the germinal disc, which will reduce hatchability.
The temperature of the farm egg storage room should higher than the egg transport truck and the egg transport truck temperature should be higher than the hatchery egg storage room. This consistent decrease in temperature is to prevent condensation (also referred to as sweating) on the eggs. Condensation on the eggshell impairs the natural mechanisms of defense and provide an ideal environment for bacteria grow, penetrate the shell, and contaminate the egg. Condensation on eggs is more common in hot and humid climates common throughout Asia.
Egg storage rooms are important, yet they are frequently overlooked. Areas to consider include:
- Consistent temperature 24/7 (insulation will minimize variation),
- Temperature alarm system – set for a maximum temperature of 21°C and a minimum of 16-18 °C,
- Temperature and humidity sensor placement – don’t place in a direct line of temperature or humidity sources as this will lead to false readings,
- Do not place sensors against walls,
- Sensor accuracy (loggers are recommended),
- Fans to evenly distribute air,
- Do not place eggs directly against the wall or on the floor in the storage room to maximize air circulation and to ensure uniform conditions, and
- Avoid direct air flow onto eggs from fans, room coolers and/or humidifiers, as this can increase moisture loss and cause temperature variation throughout the room.
The farm is the starting point to ensure chick quality. Attention to detail and hygiene throughout the whole process is critical. Through monitoring and auditing, areas with deficiencies can be identified and corrected to continue producing high quality hatching eggs.